Production Work Order Format
To keep track of orders and the supplies needed for production, use the customizable Production Work Order Formats by Vyapar. It streamlines the procedure and facilitates simple Work Order Management for you. Try any of the work order formats right away because they are all free!
- ⚡️ Create professional work order with Vyapar in 30 seconds
- ⚡ Share work order automatically on WhatsApp and SMS
- ⚡️ Connect with your parties through reminders, greetings, business cards and more
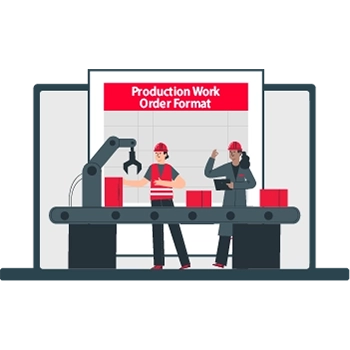
Download Production Work Order Format in Excel
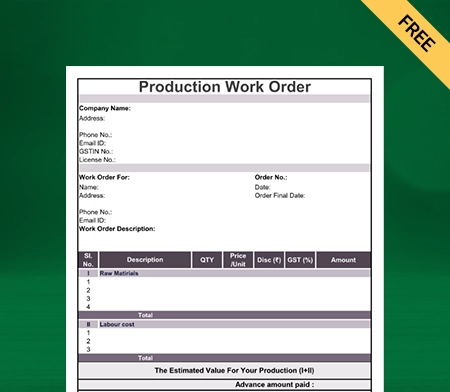
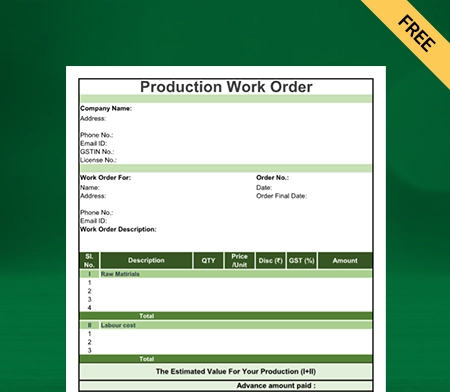
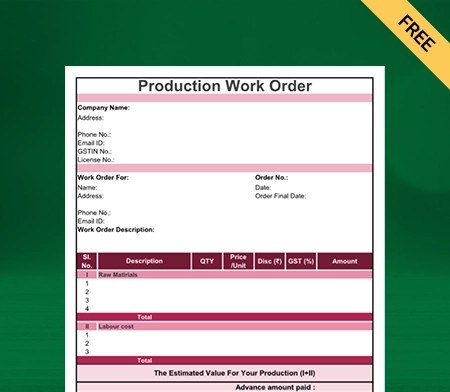
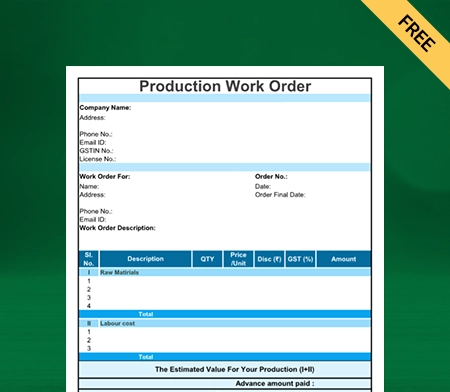
Download Production Work Order Format in PDF
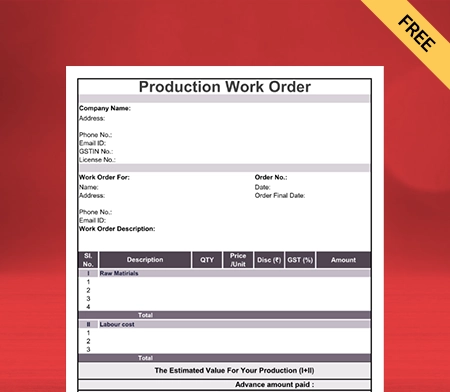
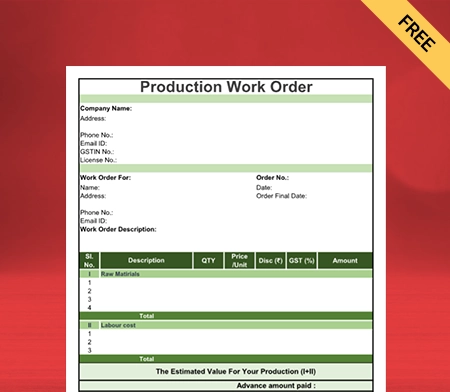
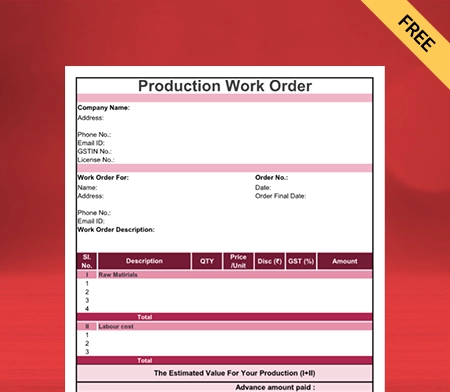
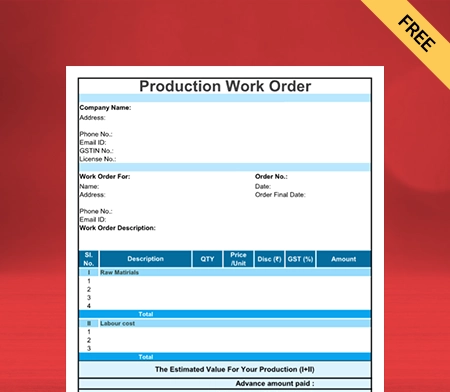
Download Production Work Order Format in Word
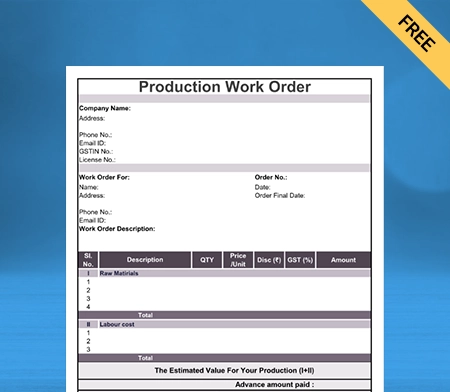
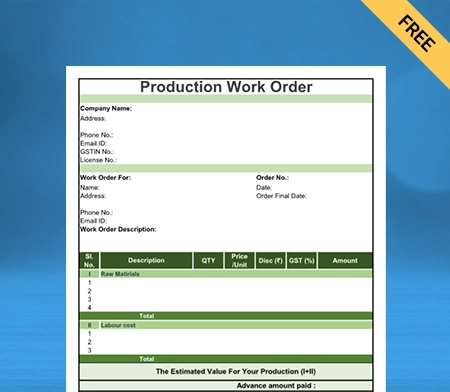
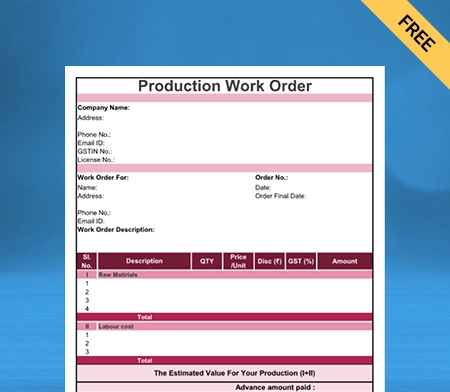
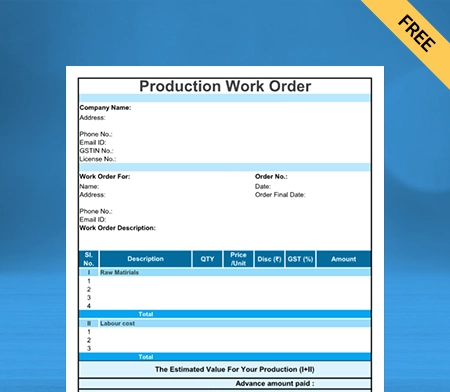
Download Production Work Order Format in Google Docs
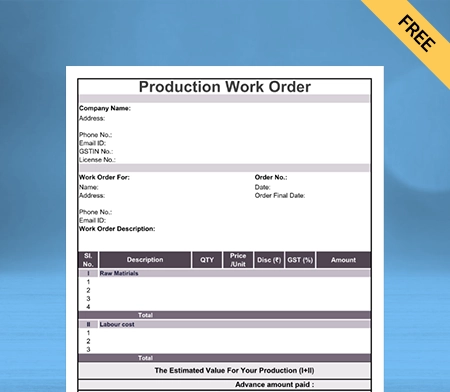
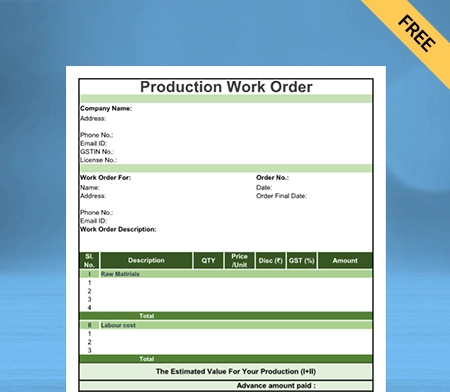
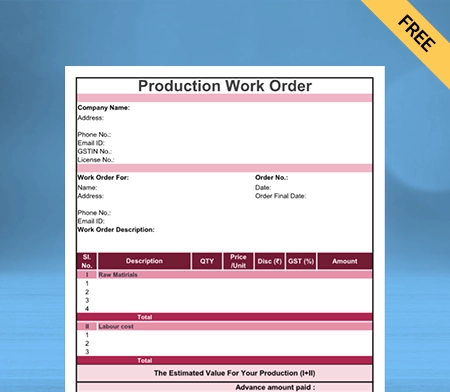
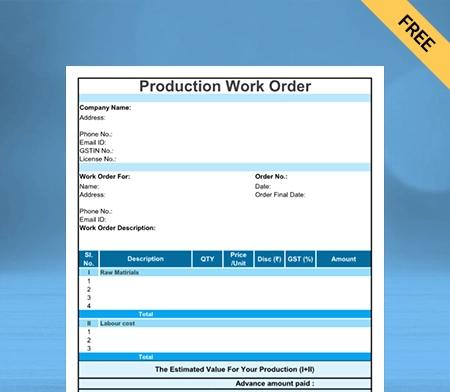
Download Production Work Order Format in Google Sheets
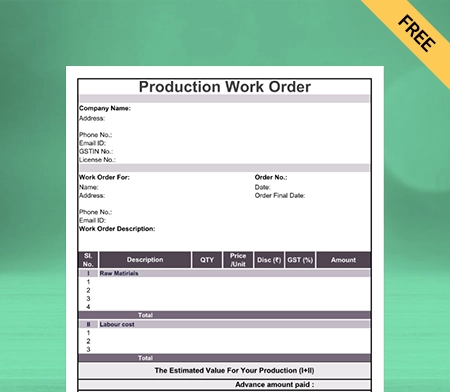
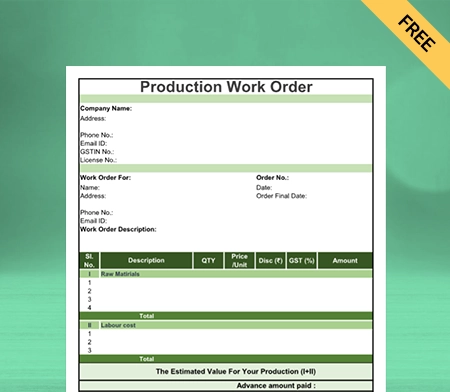
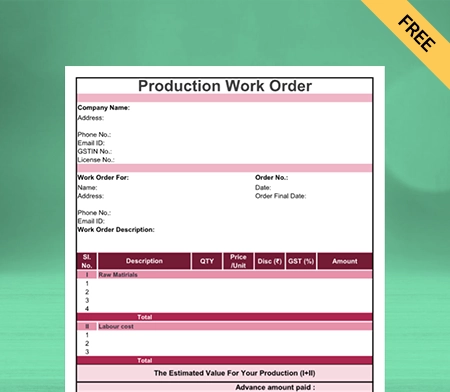
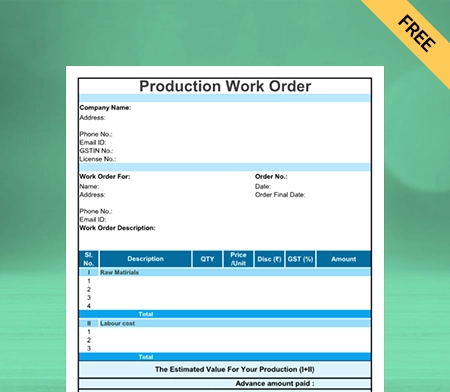
What is the Production Work Order?
A Production Work Order is a request to produce goods of a certain quantity. It is a document that outlines the details of a manufacturing or production process. It contributes to streamlining the manufacturing process, boosting output, and lowering product faults.
The Production Work Order includes details about the materials needed, the manufacturing procedures used, the number of goods to be produced, and the projected completion date.
Typically, a Production Work Order serves as a guide for workers to follow during the production process. It helps ensure that products are manufactured consistently and to a high standard.
In general, a Production Work Order can be created by a production manager or planner. It is typically issued to the workers responsible for the production process.
Why are Production Work Orders Used?
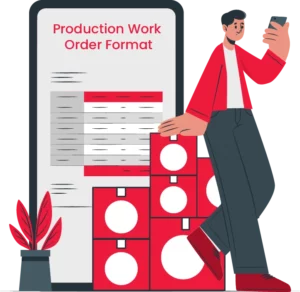
Production work orders are used to manage and track the production process of goods or services. Work orders ensure that your production process runs smoothly, efficiently, accurately, and on time.
A Production Work Order is a document that provides instructions to workers on how to manufacture or assemble a product. Here’s how you can use a Production Work Order:
Review The Work Order:
First, review the job order to ensure you understand the instructions, including the materials needed, the process’s steps, and any required quality control checks.
Collect Materials:
You must gather all the supplies needed to finish the process, which includes raw materials, tools, and equipment. The use of materials is essential to the production process. So, you must make sure you have adequate raw materials to finish the production.
Follow Instructions:
Follow the instructions in the Work Order to manufacture or assemble the product. It is essential to complete each step correctly and in the job order specified to ensure the product’s quality and consistency.
Perform Quality Control Checks:
Per the Work Order, perform quality control checks at designated checkpoints to ensure the product meets the required standards.
Complete The Work Order:
You must finish the Work Order by noting the time it took to accomplish the task, any issues encountered, and any process modifications made after assembling the product and carrying out all quality control tests.
Return Completed Work Order:
Return the completed job order to the supervisor or appropriate department to verify the product was manufactured or assembled correctly. Using a Production Work Order involves carefully following instructions and performing quality control checks to ensure the product meets the required standards.
Purpose Of Production Work Order Format:
Here are some of the key purposes of using Production Work Orders:
- Production Work Orders help ensure products are manufactured or assembled consistently and to the required standards. By providing detailed instructions, workers can ensure that each product is made the same way, regardless of who is working on the job.
- Production Work Orders can be used to monitor each job’s development. It includes data on the length of time needed to accomplish the task, any issues encountered, and process modifications implemented. The procedure can be improved by using this information to spot roadblocks.
- Maintenance Work Orders specify the materials needed to complete the job, which helps manage inventory. Manufacturers can ensure they have enough materials to complete future jobs by keeping track of the materials used for each job.
- Production Work Orders can include safety instructions to ensure workers use equipment and materials safely. It reduces mistakes and cuts down on the amount of time needed to perform the task.
- Production Work Orders help improve the efficiency of the manufacturing or assembly process by providing clear instructions on producing a product. It reduces errors and minimizes the time needed to complete the job.
- Production Work Orders include quality control checks at various stages of the manufacturing or assembly process. It ensures that the product meets the required standards and quality, reducing the risk of defects and customer complaints.
- Maintenance Work Orders help to control costs by specifying the resources required for each job. It allows manufacturers to calculate the cost of production accurately. They can make informed decisions on pricing and profitability.
- Production Work Orders manage a product’s manufacturing or assembly process. It provides detailed instructions for workers. It includes the materials needed, the steps involved in the process, and any quality control checks that workers need to be performed.
Contents of a Production Work Order Format:
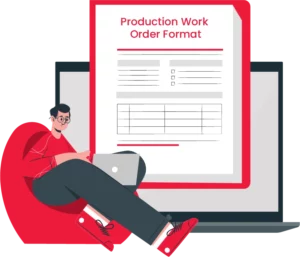
A Production Work Order Format may differ depending on the specific company requirements. It should include the following information:
Name Of The Company:
A Production Work Order Format must contain your business’s name and logo. You must also mention your address and phone number.
Customer’s Name:
The format must include the customer’s name who has requested the production of the goods.
Production Work Order Number:
An order number is a unique identifier that helps track future goods sales.
Product Details:
Your product details must include a description of the product to be produced. It should include relevant specifications such as size, shape, or colour.
Quantity:
A Production Work Order must include the number of product units produced.
Materials:
You must include a list of the materials and the quantity required for the production process in the order format.
Bill Of Materials:
A detailed list of all the components and parts required to manufacture the product.
Work Instructions:
A production work order format also contains a step-by-step guide on performing the production process, including any instructions or procedures that must be followed.
Production Schedule:
A timeline for completing the Work Order, including starting date and any deadlines or milestones.
Quality Control:
You must record any quality control checks or inspections that must be carried out during production.
Signatures:
Your format must have a section for the worker responsible for carrying out the Work Order to sign off once completed.
How to Create a Production Work Order Format Using the Vyapar App?
Here are the steps to create a Production Work Order Management format using Vyapar software:
- Open the Vyapar software with your login ID and password on your computer or mobile device.
- Choose a “Production Order” from the list of Work Order templates available.
- Fill out the forms with the necessary information for the production order. You should include information such as the production order number, the order date, the product name, and the estimated number of units to be produced.
- Next, list the raw materials required for the production process by clicking “Add Material.” Enter the name of the raw material, the quantity required, the price, and the unit of measurement.
- You can also add additional notes for the production team by clicking the “Add Instructions” button.
- Once you have added all the necessary details, click the “Save” button to create the Work Order.
- You can then view, print, or email the Production Work Order forms.
Benefits Of Using Production Work Order Format By Vyapar
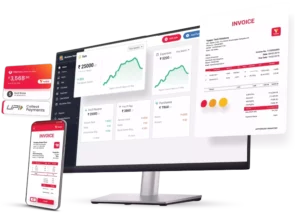
A Production Work Order Format is useful for several reasons:
Maintains Quality Consistency:
A Production Work Order Format serves as the foundation for the production process. It assures that all items, regardless of who works on them, are created to the same level.
A Production Work Order Format can ensure that products are manufactured consistently to a high standard, reducing the likelihood of defects or errors by providing detailed instructions and quality control measures.
You can save the Production Work Order Format for the future once you customize it. This way, you don’t have to make a Maintenance Work Order form every time from scratch. You can avoid confusion and maintain consistency by issuing similar orders to your clients.
Helps Stay Organised:
A Production Work Order Format provides a structured approach to the manufacturing process, making it easier to organize the various tasks and ensure that all necessary steps are completed correctly.
By breaking down the manufacturing process into clear, sequential steps, a Production Work Order Format helps ensure workers stay organized and focused.
When you write Maintenance Work Order Formats manually, you might make errors. The ready-made Production Work Order Format eliminates errors and expedites the process.
Useful In Record-Keeping:
Production Work Order forms provide a record of the work that has been completed, including any materials used, the time and resources required, and any issues or challenges that arose during the process.
This documentation can be valuable for future reference, troubleshooting, and planning. Work Order Formats play a crucial role in standardizing the process of requesting, assigning, and tracking work tasks.
By using a consistent format, everyone involved in the work process can understand what needs to be done. Every employee knows who is accountable for work and when the timeline is to get the work done.
Promotes Work Transparency:
A Production Work Order Format clearly and concisely communicates essential information about the manufacturing process to all parties involved.
Using Work Order Management Software helps ensure that everyone involved in the production process can access the same information, reducing the likelihood of miscommunication or errors.
Additionally, it includes instructions and guidelines for quality control checks. It helps to ensure that all products meet the required quality standards.
Increases Work Efficiency:
By outlining the steps involved in the production process and providing a clear timeline, a Production Work Order Format can improve efficiency and reduce downtime, allowing products to be manufactured more quickly and at a lower cost.
A Maintenance Work Order Format provides a clear record of the manufacturing process, making it easier to track progress, identify areas for improvement, and maintain compliance with regulatory requirements.
A Production Work Order Format can help improve productivity, quality, and efficiency in a manufacturing or production environment, leading to better outcomes for the business and its customers.
Customized Work Order Format:
A customized Production Work Order Format can give a business a more polished and organized appearance. It demonstrates the company’s attention to detail and seriousness about its financial obligations.
Using a standardized and customized Maintenance Work Order Format can enhance a company’s brand image. It demonstrates that the business pays close attention to every facet of its operations and maintains a consistent brand identity across all platforms.
Customized Production Work Order Format can incorporate a business’s logo, brand colours, and other visual cues, which can help stakeholders like workers, suppliers, and contractors better recognize and understand the brand.
Features Of The Vyapar App That Help Manage Production Work Orders Effectively:
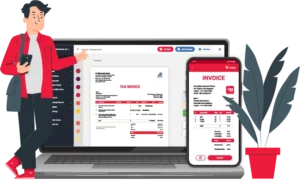
Vyapar has amazing features that can help you with daily accounting and billing software. You can track orders and sales with the help of our Inventory Management Software. Here is a list of a few features:
Maintain Inventory Efficiently:
Maintaining the raw materials inventory for production to go seamlessly is essential. Manufacturers can enhance their performance using the free Work Order Management feature from Vyapar.
You can keep tabs on your company’s sales. You may see the current state of your inventory. Also, you can set up alerts to inform your suppliers of any new orders. It will be simpler to evaluate how successfully you have managed your inventory.
By implementing inventory tracking tools, businesses can optimize inventory space utilization to its fullest extent. You can save space by eliminating items that sell less frequently using the analysis.
The tracking process utilizes information such as batch number, expiration date, manufacturing date, slot number, and more. Having the necessary goods on hand and ready to buy when needed is beneficial. Also, inventory management helps to keep track of everything so that no theft goes unreported.
Make Reports Within Minutes:
Business reports are an essential source of information. They keep everyone updated on the ongoing and completed activities. You can create 40+ business reports using the Vyapar app.
Vyapar Billing and Management Software provides you with different format choices. You can create sales reports, production reports, financial records, and many other reports.
Analysing reports can give you an accurate and fair perspective of your business. It can increase your business’s operational efficiency. Additionally, it also enhances your team’s productivity.
Furthermore, it is a rapid and effective method of determining profitability. Users can immediately inspect and analyse the data. The Management Software lets you make graphical reports to track sales and expenses.
Seamless Bank Account Management:
You can send or receive money using bank accounts and conduct bank-to-bank transfers for simple cash flow management. The Vyapar invoicing software is the best since businesses can use it for all their cash-ins and cash-outs.
A business bank account must be linked to the Vyapar Accounting Software to use the bank accounts feature. The Vyapar app simplifies managing liability, O.D., and credit card accounts. You can easily make a deposit and withdraw funds from bank accounts.
Payments may be added, managed, and tracked rapidly for online and offline enterprises. You may effortlessly enter data into the free Management Software regardless of whether your revenue comes from banks or e-wallets.
You may control cheque payments using free accounting software from Vyapar and manually change the amount. Open checks are available on the Vyapar App, allowing users to deposit or withdraw money and immediately cancel them.
Manage All Orders:
With Vyapar, making sales orders and purchase orders is effortless. Setting up a due date for orders becomes easy with it. An automatic stock adjustment is also provided. It helps to guarantee that inventory goods are available.
Tracking prevents losses. With monitoring, you may save time and use it towards other regular activities. More satisfied customers are the result. The app lets you track when payment is due and attach a tax invoice to your order.
It is also simpler to upgrade your sale and purchase order formats. Options available on the Vyapar App include Word, PDF, and Excel. You can reduce labour costs and time by using our GST invoicing software.
With automation, you can quickly convert orders to sale/purchase invoices. Using our free billing software, you can keep track of open, closed, and late charges. Businesses can easily track everything by utilising these features.
Protect Business Data:
Making backups is essential to ensure the protection of all data. To ensure the security of the data stored in the application, Vyapar allows you to configure an automatic data backup.
Data security is crucial because it is the basis of all modern enterprises. By generating automatic backups or setting up secure backups on schedule, you can protect the security of your business.
Occasionally, you can create a local backup to safeguard your data in a private area, such as a pen drive or hard disc. It provides an additional layer of security for your data.
You may analyse your sales data whenever you need to use the accounting tools in the Vyapar Management Software. After reviewing the financial reports, the Vyapar accounting app produces, you can create a business strategy.
Track Your Expenses:
Keeping track of and recording all expenditures made throughout the production process is essential for adequately preparing your accounting and taxes. With Vyapar, creating accurate reports and keeping tabs on expenses is easy.
Raising revenue and saving expenditures is feasible by keeping track of spending. Using the free programme, you can quickly keep track of unpaid commitments. Also, it helps them track their material in the future.
Budgeting is easy with the help of our free software. Businesses may rapidly reduce expenses and save a sizable sum of money. Using our billing software, you can keep track of GST and non-GST spending.
We have specifically developed the Vyapar app to cater to the needs of small and medium-sized businesses. It offers a free and user-friendly solution on smartphones. They are, therefore, capable of managing both received and spent funds. Also, keeping track of your expenses will make it simpler to develop practical solutions.
Frequently Asked Questions (FAQs’)
A Production Work Order Format serves as a structured document utilized in manufacturing and production industries to convey precise details about a production process. It guides workers during manufacturing, outlining the materials, equipment, instructions, and other essential information needed to produce a product.
A Production Work Order Format ensures that manufacturing processes run smoothly and efficiently, leading to consistent, high-quality products and a more profitable business.
A Production Work Order Format must include the following information:
1. Title and details of the assignment
2. Name and contact details of the person or company that requested production
3. Completion date
4. Details of materials required
5. Prices
6. Taxes
7. Signature
You can use the Vyapar format generator to create a Production Work Order Format. Include all the Work Order details and save it as your standard template. You can also choose any template layout provided by Vyapar and customize it to meet your needs.
Yes. You can customize your Production Work Order Format using Work Order templates provided by Vyapar. You can add colours, rows, columns, your business logo, and other things to meet your needs.
Here are some best practices for using a Production Work Order Format:
1. Keep your Production Work Order Format simple.
2. Provide clear instructions for each task.
3. Ensure to include all the essential details in the Production Work Order Format.
4. Keep track of all the progress.
Using a Production Work Order Format, you can establish a consistent procedure for every job, reducing the chances of errors. It provides a guide to workers and helps them complete their tasks quickly.
Using a Production Work Order Format for every project is unnecessary. However, using a format helps you define work, assign jobs, track progress, and stay organized.
Related Posts:
1. Retail Inventory Software Macbook
2. Bill of Exchange Format
3. Product Costing Format
4. Fabrication Work Quotation Format
5. Building Estimate Format in PDF